編輯導(dǎo)語(yǔ):介紹了高速?zèng)_床球墨鑄鐵圓盤(pán)鑄件的化學(xué)成分、造型工藝、澆注系統(tǒng)與冷鐵、球化與孕育處理、熔煉澆注等工藝方案。采用AnyCasting軟件對(duì)充型和凝固過(guò)程的進(jìn)行了模擬分析。通過(guò)生產(chǎn)驗(yàn)證獲得了金相組織和力學(xué)性能滿(mǎn)足要求的鑄件。分析認(rèn)為,對(duì)于沖床類(lèi)鑄件化學(xué)成分應(yīng)控制碳當(dāng)量4.0%~4.2%、硅2.1%~2.3%、錳≤0.5%,殘余鎂含量0.035%~0.055%,稀土0.01%~0.02%;采用多次孕育,選取釔基重稀土球化劑,縮短凝固時(shí)間;采用底注多內(nèi)澆道分散設(shè)置,保證鐵液充型平穩(wěn),冷鐵加強(qiáng)關(guān)鍵部位冷卻,減少縮松缺陷,提高鑄件的組織致密度和力學(xué)性能。
圓盤(pán)鑄件是高速?zèng)_床至關(guān)重要的部件,高速?zèng)_床的主體由飛輪圓盤(pán)組成,其周面上設(shè)有若干方槽,主要起減重作用,圓盤(pán)底部設(shè)有6個(gè)工藝孔,與筋板連接處為圓弧段,為了確保沖床沖壓力度始終均勻,延長(zhǎng)其使用壽命,圓盤(pán)不能變形。
圓盤(pán)毛坯質(zhì)量38 000 kg,三維結(jié)構(gòu)見(jiàn)圖1所示,鑄件總高度1 700 mm,圓盤(pán)外徑4 800 mm,最大尺寸5 820 mm,主要壁厚為220 mm,軸承座孔根部壁厚最大,屬于熱節(jié)區(qū)域。圓盤(pán)材質(zhì)為QT500-7,單鑄試棒要求力學(xué)性能為抗拉強(qiáng)度大于420 MPa,屈服強(qiáng)度大于320 MPa,斷后伸長(zhǎng)率大于5%。鑄件下表面有一圈螺紋孔,與蓋配合,要求孔內(nèi)無(wú)疏松缺陷。因鑄件空腔面積大,鑄造工藝?yán)щy。
球墨鑄鐵具有較大的氧化傾向,為保證鐵液充型平穩(wěn)防止湍流、減少夾渣和氣孔等缺陷,大型鑄件一般采用底注式、半封閉式澆注系統(tǒng),另外圓盤(pán)鑄件模數(shù)較大,理論上通過(guò)保證樹(shù)脂砂砂型強(qiáng)度、加強(qiáng)鐵液隨流孕育等措施,可達(dá)到無(wú)冒口鑄造。根據(jù)碳當(dāng)量CE決定C和Si的含量,一般來(lái)說(shuō)選擇C含量為3.5%左右。P是正偏析元素,又是促進(jìn)碳化物形成元素,含量應(yīng)盡可能低,要求P≤0.02%。不同的S含量,所需的Mg殘量是不同的,只有低的S含量才能保證在較低的Mg殘含量(0.035%~0.055%)下獲得2級(jí)以上的球化效果,一定要保證原鐵液的S<0.015%,最好控制在0.01%以下。
消耗Mg類(lèi),如Ti、S、O、Te、Se等元素。消耗Mg或在石墨球長(zhǎng)大過(guò)程中直接干擾Mg的球化作用;正偏析碳化物形成元素,如Mn、Cr、Mo、V、P等。對(duì)于大斷面球墨鑄鐵來(lái)說(shuō),加入微量干擾元素(如Sb、Bi等),不但對(duì)球化沒(méi)有影響,還能增加石墨球數(shù)和球化率,消除碎塊狀石墨,一般加入量控制在0.005%~0.01%,因超過(guò)此含量,則其破壞球化的作用又表現(xiàn)出來(lái)。具體工藝設(shè)計(jì)的化學(xué)成分如表1所示:
表1 化學(xué)成分(質(zhì)量分?jǐn)?shù),%)

采用呋喃樹(shù)脂砂,三箱造型,分型方式如圖2所示。澆冒口系統(tǒng)工藝設(shè)計(jì)示意圖見(jiàn)圖3。
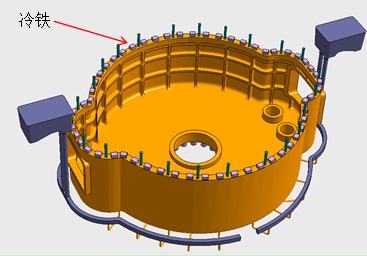
為保證圓盤(pán)底面的材料致密性,同時(shí)使得鐵液充型平穩(wěn),減少?zèng)_砂風(fēng)險(xiǎn),將底面置于下箱,金屬液通過(guò)內(nèi)澆道從圓盤(pán)底面注入。為減少澆注系統(tǒng)與砂型的碰撞,使用隨型橫澆道。
大模數(shù)球墨鑄鐵的凝固時(shí)間長(zhǎng),常會(huì)降低石墨球化率,或?qū)е率?、石墨漂浮、石墨粗大等缺陷,故需采用冷鐵縮短其凝固時(shí)間。圓盤(pán)熱節(jié)主要集中在底部,如圖3所示,由于結(jié)構(gòu)限制,不適合放置冒口,于是在工藝設(shè)計(jì)時(shí),以冷鐵為主,針對(duì)厚大斷面球墨鑄鐵件的鑄造,冷鐵的使用非常關(guān)鍵,不僅可以加強(qiáng)冷鐵附近區(qū)域鑄件的冷卻,改善金相組織,防止石墨衰退,另外在充型時(shí),不斷降低相接觸鐵液的溫度,讓鐵液的液態(tài)收縮提前,從而得到澆注系統(tǒng)的及時(shí)補(bǔ)縮,盡量減小鑄件在澆注系統(tǒng)凝固后的收縮量。
采用球墨鑄鐵大件工藝設(shè)計(jì)原則,澆注鐵液的質(zhì)量約為40 000 kg,最終選取的澆注系統(tǒng)各單元截面比例約為A直:A橫:A內(nèi)=1:1.2:0.8,用以保證鐵液大流量、平穩(wěn)。
厚大斷面球墨鑄鐵件,因其球化衰退導(dǎo)致產(chǎn)生石墨畸變及碎塊狀石墨,數(shù)據(jù)表明Mg殘含量提高至0.05%~0.07%,結(jié)果并不理想,Mg殘含量的增加反而使球墨鑄鐵的縮松與夾渣廢品顯著上升。因此,厚大斷面球墨鑄鐵最后凝固的球化衰退不能用Mg的逃逸衰退來(lái)解釋?zhuān)渲饕蚴桥c球墨鑄鐵中的S含量有關(guān),S含量越高球化衰退越快,反之越慢,因此將S含量控制在較低水平是抗球化衰退的重要措施,在保持一定的Mg殘含量的情況下,將球化后S含量控制在0.006%~0.01%。對(duì)于圓盤(pán)鑄件,采用沖入法球化。球化劑選用釔基重稀土球化劑,主要元素及加入量見(jiàn)表2所示。
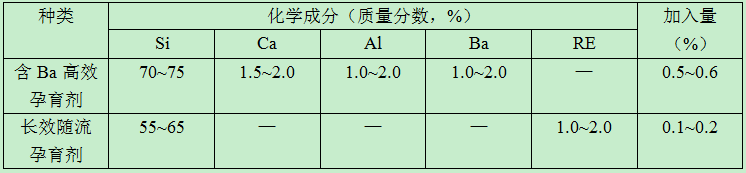
厚大斷面球墨鑄鐵件的多次孕育與中小球墨鑄鐵件孕育有3點(diǎn)不同:一是出鐵孕育時(shí)孕育量大;二是澆包是20~60 t的大包,孕育后難以攪拌;三是澆注時(shí)由于鐵液量多達(dá)幾十噸,隨流孕育難度大。孕育是防止厚大斷面球墨鑄鐵石墨畸變、出現(xiàn)碎塊狀石墨的有效措施。孕育時(shí)需要注意兩個(gè)問(wèn)題:一是原鐵液中S的含量不能過(guò)低,應(yīng)大于0.006%,鐵液中O的含量不能過(guò)低,應(yīng)大于0.001%,否則影響孕育效果;二是控制Si總的含量不可過(guò)高,因?yàn)榍蚧瘎┲械腟i含量一般為45%左右,孕育劑中的Si含量大于70%。采用多次孕育處理,選用含Ba高效投擲孕育劑和長(zhǎng)效隨流孕育劑,主要元素及加入量見(jiàn)表3所示。
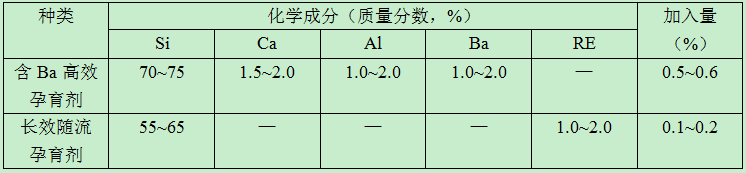
低溫澆注能縮短厚大球墨鑄鐵件凝固時(shí)間,改善其石墨形態(tài),在實(shí)際生產(chǎn)中,為了獲得低的澆注溫度而又不至于加長(zhǎng)鐵液保持時(shí)間引起孕育衰退,采用倒包等措施使鐵液快速降溫。圓盤(pán)的熔煉溫度控制在1 500~1 550 ℃,過(guò)熱靜置5~8 min,凈化鐵液,出爐溫度控制在1 430~1 460 ℃,為縮短凝固時(shí)間,同時(shí)減小液態(tài)收縮,可適當(dāng)降低澆注溫度,但過(guò)低的澆注溫度不利于鐵液中的夾渣和氣體等上浮,甚至形成冷隔,因此綜合考慮將澆注溫度定為1 300~1 330 ℃。
采用AnyCasting軟件對(duì)鑄造工藝進(jìn)行充型和凝固過(guò)程的模擬,模擬結(jié)果顯示鐵液進(jìn)入型腔后,充型無(wú)較明顯飛濺,較為平穩(wěn);充型40%時(shí),鑄件內(nèi)鐵液平均速度為51 cm/s,趨于平穩(wěn),無(wú)沖砂風(fēng)險(xiǎn);充型結(jié)束時(shí),氧化夾雜風(fēng)險(xiǎn)降低;鐵液溫度下降50 ℃,溫差較小,無(wú)冷隔風(fēng)險(xiǎn)。
圖4為充型順序的仿真結(jié)果,從圖中可以看出,金屬液充填12 s時(shí),內(nèi)澆道進(jìn)水口處存在孤立液相島,有噴濺傾向,此處與內(nèi)澆道末端時(shí)間相差24 s,較為安全。充型43 s時(shí),鐵液到達(dá)型腔各位置時(shí)間較為均勻,充型平穩(wěn)。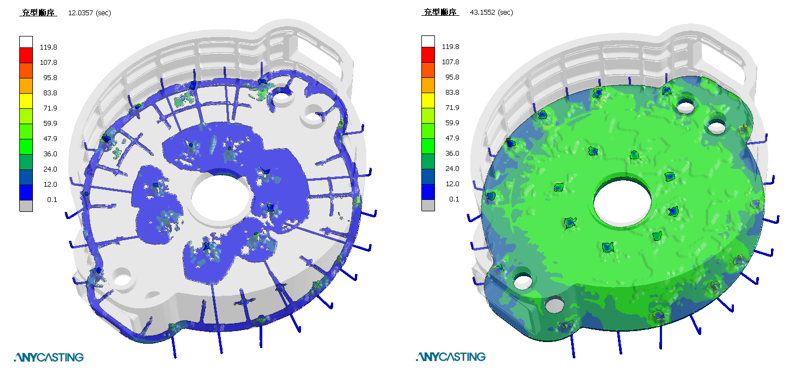
(a)金屬液充填12s時(shí)的模擬結(jié)果 (b)金屬液填充43s時(shí)的模擬結(jié)果
圖5為充型速度場(chǎng)的仿真結(jié)果,從圖中可以看出,充型14%時(shí),內(nèi)澆道進(jìn)水口處速度160 cm/s,速度適中,充型40%時(shí),鑄件內(nèi)平均速度為51 cm/s,速度趨于平穩(wěn),無(wú)沖砂風(fēng)險(xiǎn)。
(a)充型14%時(shí)的速度場(chǎng) (b)充型40%時(shí)的速度場(chǎng)
圖6為充型過(guò)程中氧化物的仿真結(jié)果,從圖中可以看出,充型17%時(shí),軸承座孔工藝臺(tái)氧化物含量4.2 g/cm3,存在氧化夾雜風(fēng)險(xiǎn),充型結(jié)束時(shí),鑄件上表面氧化物含量3.58 g/cm3,氧化夾雜風(fēng)險(xiǎn)降低。
(a)充型17%時(shí)的氧化物 (b)充型100%時(shí)的氧化物
圖6 充型過(guò)程中氧化物的模擬結(jié)果
圖7為充型溫度場(chǎng)的仿真結(jié)果,從圖中可以看出,充型至26%時(shí)鐵液溫度下降30 ℃,充型結(jié)束時(shí)鐵液溫度下降50 ℃,溫差較小,無(wú)冷隔風(fēng)險(xiǎn)。
(a)充型26%時(shí)的溫度場(chǎng) (b)充型100%時(shí)的溫度場(chǎng)
圖7 充型溫度場(chǎng)的模擬結(jié)果
按照上述工藝過(guò)程進(jìn)行試制,獲得鑄件的化學(xué)成分、力學(xué)性能和組織的檢測(cè)結(jié)果見(jiàn)表4、表5和圖8。
表3 鑄件的化學(xué)成分(質(zhì)量分?jǐn)?shù),%)

表4 圓盤(pán)附鑄試樣的組織和力學(xué)性能

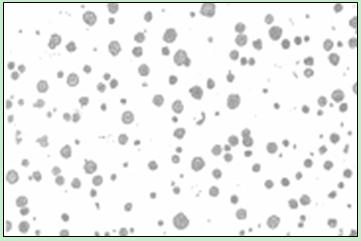
(a)腐蝕前金相
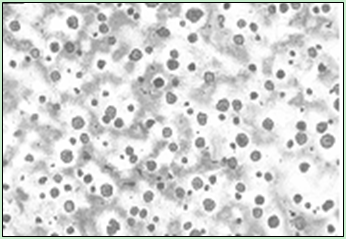
圖8 圓盤(pán)附鑄試樣的金相組織(100×)
試驗(yàn)結(jié)果顯示,附鑄試塊性能達(dá)到技術(shù)要求,首件經(jīng)機(jī)加工驗(yàn)證無(wú)缺陷,鑄件成品如圖9所示,并通過(guò)工藝過(guò)程評(píng)定后,最終對(duì)其鑄造工藝進(jìn)行固化。
(1)對(duì)于沖床球墨鑄鐵圓盤(pán)鑄件,合適的化學(xué)成分(質(zhì)量分?jǐn)?shù))為碳當(dāng)量4.0%~4.2%、硅2.1%~2.3%、錳≤0.5%,殘余鎂含量控制在0.035%~0.055%,稀土元素控制在0.01%~0.02%。(2)采用多次孕育,選取釔基重稀土球化劑,出爐溫度控制在1 430~1 460 ℃,縮短凝固時(shí)間,可以改善石墨球分布及形態(tài)。(3)針對(duì)大型球墨鑄鐵件,盡量采用底注多內(nèi)澆道分散設(shè)置,保證鐵液充型平穩(wěn),冷鐵加強(qiáng)關(guān)鍵部位冷卻,消除或減輕縮松缺陷,提高鑄件的組織致密度和力學(xué)性能。