編輯導(dǎo)語:大型托輪在生產(chǎn)時(shí),經(jīng)粗加工后經(jīng)常出現(xiàn)嚴(yán)重缺陷,甚至導(dǎo)致托輪報(bào)廢,造成重大損失。介紹了大型托輪鑄造生產(chǎn)時(shí)容易出現(xiàn)的氣孔掉砂、超探不合格、裂紋等缺陷,并對(duì)其進(jìn)行分析,在鑄造工藝技術(shù)、設(shè)計(jì)結(jié)構(gòu)優(yōu)化、生產(chǎn)過程控制等方面進(jìn)行了探索性實(shí)踐。采取優(yōu)化措施后,生產(chǎn)的上百件大型托輪質(zhì)量得到明顯改善,避免了重大缺陷,降低了返修成本,并縮短了返修周期,取得了顯著的經(jīng)濟(jì)效益,相關(guān)經(jīng)驗(yàn)可供參考。
工業(yè)回轉(zhuǎn)窯廣泛地應(yīng)用于水泥、冶金球團(tuán)、活性石灰、化工等行業(yè)。托輪是其核心零件之一,通過和窯體輪帶的對(duì)滾運(yùn)動(dòng),承受了整個(gè)窯體的重量,且長(zhǎng)期處于高溫、高負(fù)荷的交變應(yīng)力狀態(tài)下的工作環(huán)境,因此對(duì)其內(nèi)部質(zhì)量的要求十分嚴(yán)格。托輪材質(zhì)一般采用鑄鋼進(jìn)行生產(chǎn),不允許存在明顯的鑄造缺陷,技術(shù)要求規(guī)定為超聲波探傷按GB/T 7233.1-2009中2級(jí)執(zhí)行,磁粉探傷GB/T 9444-2007中2級(jí)執(zhí)行。隨著現(xiàn)代工業(yè)的快速發(fā)展,同時(shí)根據(jù)國(guó)家產(chǎn)業(yè)政策上大壓小的指導(dǎo)方針,回轉(zhuǎn)窯的規(guī)格也逐步增大,以水泥窯為例,目前已普遍達(dá)到日產(chǎn)5 000 t以上,同時(shí)萬噸窯也在不斷興建。而托輪規(guī)格也隨之增大,由以往的φ1.8 m以內(nèi)躍升至φ2 m以上,最大的托輪目前已達(dá)到φ3.3 m,毛重達(dá)80t以上。筆者根據(jù)實(shí)際生產(chǎn)情況,將φ2 m以上托輪暫定為大型托輪。
托輪材質(zhì)一般選擇ZG42Cr1Mo、ZG35Cr1Mo或相近材料,外圓硬度一般在220~240 HBW左右,生產(chǎn)流程為冶煉→鑄造→保溫→落砂→鑄后高溫退火→熱割冒口→去應(yīng)力回火→毛坯精整→粗加工→無損檢測(cè)→(缺陷返修)→調(diào)質(zhì)熱處理→半精加工→無損檢測(cè)→精加工。托輪的鑄造工藝方案較為成熟(見圖1),主要內(nèi)容具體如下:(1)采用單個(gè)冒口,中心軸孔上部鑄實(shí)作為補(bǔ)縮通道。(2)外圓采用整圈冷鐵激冷,促進(jìn)形成凝固末端,同時(shí)提升外圓關(guān)鍵使用面的致密度,進(jìn)而提高疲勞強(qiáng)度,達(dá)到提高與輪帶對(duì)滾運(yùn)行中耐磨性的效果。(3)采用對(duì)應(yīng)外輪緣底返切澆注+補(bǔ)澆冒口的澆注方案,以保證前期快速平穩(wěn)充型,后期改善冒口中鋼液的溫度梯度,提高冒口補(bǔ)縮能力。
(a)鑄造工藝圖 (b)帶冒口鑄件三維圖
某廠在采用通用工藝方案生產(chǎn)托輪時(shí),質(zhì)量無法保證穩(wěn)定,尤其在大型托輪生產(chǎn)時(shí),粗加工后經(jīng)常發(fā)現(xiàn)嚴(yán)重缺陷,甚至導(dǎo)致報(bào)廢,造成重大損失。嚴(yán)重缺陷主要為大面積氣孔掉砂、超探不合格、裂紋三類,如圖2所示。
(b)粗加工后暴露的內(nèi)孔裂紋
(d)水口端面超探缺陷
當(dāng)托輪出現(xiàn)嚴(yán)重缺陷時(shí),由于材質(zhì)為低合金鋼,后續(xù)還需進(jìn)行調(diào)質(zhì)處理,其焊補(bǔ)工藝十分復(fù)雜,需要較高的預(yù)熱及焊后回火溫度,同時(shí)為保證焊補(bǔ)區(qū)探傷及硬度合格,對(duì)焊工的操作技能要求十分嚴(yán)格。企業(yè)需要投入大量的人力、物力進(jìn)行焊補(bǔ)返修,嚴(yán)重影響正常的生產(chǎn)進(jìn)程。當(dāng)托輪出現(xiàn)重大裂紋缺陷時(shí)往往只能報(bào)廢處理,以上問題均嚴(yán)重影響了企業(yè)的經(jīng)濟(jì)效益。
托輪外輪緣上部的砂型為封閉空間,在澆注過程中,若鋼液液面上升速度過快,則極易出現(xiàn)憋氣等現(xiàn)象,造成嚴(yán)重的氣孔缺陷。若上升速度較慢,則容易出現(xiàn)烘烤掉砂問題。因此托輪液面上升速度一般控制在8~15 mm/s。托輪澆注時(shí),當(dāng)鋼液上升至接近分型面的位置,受減重凹槽砂芯的影響,托輪水平截面積顯著減小,由此導(dǎo)致此時(shí)液面上升速度急劇加快,外輪緣上部的出氣壓力隨之增大,如果出氣孔的直徑不增加,就得增加出氣孔數(shù)量,當(dāng)出氣孔擺放數(shù)量過少時(shí),滿足不了出氣需求,容易出現(xiàn)憋氣現(xiàn)象;如果出氣孔的數(shù)量不增加,就得加大單個(gè)出氣孔的直徑,而加大出氣孔的直徑又容易形成局部小熱節(jié),進(jìn)而造成探傷缺陷。
基于上述分析,應(yīng)從澆注過程的澆注速度控制和出氣孔設(shè)置采取措施。大型托輪一般均采用雙水口澆注,在澆注前期采用雙水口全開方式,提高充型速度,當(dāng)鋼液上升至減重槽高度時(shí),應(yīng)采取控流措施,適當(dāng)降低澆注速度,如關(guān)閉一個(gè)水口,此時(shí)液面上升速度仍在合理范圍以內(nèi)。外輪緣出氣孔布置應(yīng)采用細(xì)直徑、多擺放的原則??刹捎?em style="margin: 0px; padding: 0px; outline: 0px; max-width: 100%; box-sizing: border-box !important; overflow-wrap: break-word !important;">φ25~φ35 mm的鋼管(來源廣泛)作為出氣孔,出氣孔沿圓周方向均布,出氣孔數(shù)量可按兩孔之間的圓周距離為400 mm左右較為適宜,見圖3。
4.1 原因分析
通過收集分析100余件托輪的生產(chǎn)情況,其中共有12件托輪冒口面出現(xiàn)嚴(yán)重的超探缺陷,出現(xiàn)比例約為10%,主要有以下兩個(gè)影響因素:這12件托輪的凹槽深度范圍105~300 mm,其中有10件托輪的凹槽深度超過250 mm。托輪外輪緣上端部位需冒口中的鋼液越過凹槽砂芯后,再向上充分補(bǔ)縮才能滿足內(nèi)部質(zhì)量要求。而凹槽深度越深,鋼液需克服的壓力差越大,向上補(bǔ)縮越困難,其補(bǔ)縮效果就越差,外輪緣靠近上端面部位愈容易出現(xiàn)UT缺陷,如圖4所示。
(b)托輪凝固模擬
這12件托輪中,有8件托輪的直徑都大于2 200 mm,均屬于大型托輪,其中有3件托輪為同一規(guī)格,因此以該規(guī)格托輪為例進(jìn)行分析。經(jīng)查該規(guī)格托輪同批次共需生產(chǎn)8件,圖紙尺寸為外圓φ2 500 mm,內(nèi)圓φ1 010 mm,高度1 150 mm,凹槽深度300 mm。由于現(xiàn)場(chǎng)專用冷模圈(約220 mm厚)僅有1件,每次只能生產(chǎn)一件托輪,待保溫到期脫模后,才能生產(chǎn)下一件托輪。因此為保證生產(chǎn)周期,另制模型一套,外圓砂型采用企業(yè)原有的300 mm厚度標(biāo)準(zhǔn)冷鐵造型。如圖5所示。生產(chǎn)結(jié)果顯示,以上兩種工藝方案中,采用300 mm厚度冷鐵共生產(chǎn)5件托輪,質(zhì)量良好。采用冷模圈生產(chǎn)的3件托輪,均出現(xiàn)較大超探缺陷,缺陷性質(zhì)為典型的鑄造縮松。
(b)300mm厚冷鐵生產(chǎn)托輪
托輪規(guī)格越大,外輪緣厚度越大,熱節(jié)越大,凝固時(shí)間越長(zhǎng),且托輪材料為低合金鋼,糊狀凝固特點(diǎn)更加顯著,而整圈冷鐵厚度有限時(shí),其激冷效果將低于預(yù)期目標(biāo),導(dǎo)致容易出現(xiàn)超探缺陷。
根據(jù)上述分析,大型托輪生產(chǎn)時(shí),應(yīng)采取擴(kuò)大補(bǔ)縮通道及增強(qiáng)激冷效果的措施。可通過優(yōu)化設(shè)計(jì)結(jié)構(gòu)或增加鑄造工藝補(bǔ)塊的方式,改變凹槽外形,降低凹槽深度,擴(kuò)大補(bǔ)縮通道。此外隨著托輪規(guī)格的增大,根據(jù)熱節(jié)尺寸的變化,增大冷鐵厚度,提高激冷效果。同時(shí)整圈冷鐵上端面應(yīng)與托輪分型面盡量貼齊,留夠20 mm以內(nèi)的掛砂層,提高冷鐵對(duì)上端難補(bǔ)縮部位的激冷效果。
5.1 缺陷分析
某托輪在調(diào)質(zhì)后的半精加工階段發(fā)現(xiàn)水口端面出現(xiàn)超探缺陷,缺陷的宏觀形貌為表面裂紋,為查找其產(chǎn)生原因,對(duì)缺陷處進(jìn)行了PT檢測(cè)、現(xiàn)場(chǎng)拋光打磨、金相分析,如圖6所示。
(b)水口端裂紋PT顯示
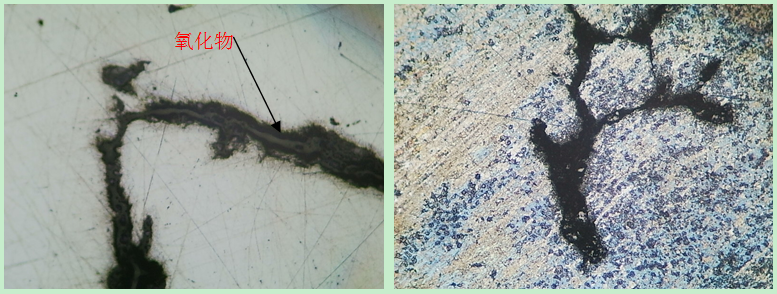
(a)裂紋沿半網(wǎng)狀或網(wǎng)狀空隙分布(100×)
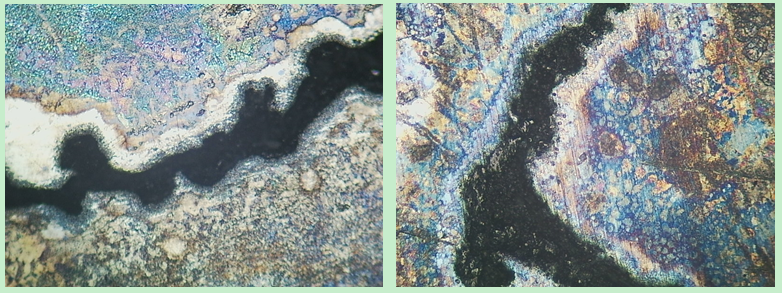
將缺陷周圍打磨拋光,在顯微鏡下觀察,裂紋空隙中存在氧化物,見圖7(a)所示,上述氧化物是在后期高溫氧化下產(chǎn)生的。根據(jù)托輪的生產(chǎn)流程,說明缺陷在調(diào)質(zhì)處理之前已經(jīng)存在。另外從圖7(a)中可以看出,裂紋均沿半網(wǎng)狀或網(wǎng)狀的空隙形態(tài)分布,為典型的鑄造縮松缺陷。用4%硝酸酒精腐蝕,可清晰觀察到裂紋兩側(cè)均存在不同程度的氧化脫碳現(xiàn)象,見圖7(b)。因此可判定,該裂紋早期為鑄造縮松缺陷,在后期的調(diào)質(zhì)處理過程中,因熱應(yīng)力作用導(dǎo)致了裂紋擴(kuò)展連接。托輪的澆注系統(tǒng)如圖8所示,為保證其快速平穩(wěn)充型的澆注工藝要求,內(nèi)澆口沿外輪緣底面向上切入。結(jié)合缺陷出現(xiàn)的位置進(jìn)行深入分析,缺陷位于外輪緣水口端面的中間部位,且分散分布,與托輪內(nèi)澆口位置重合,因此判斷上述缺陷的產(chǎn)生與澆注系統(tǒng)關(guān)系較大。
(b)托輪鑄件的澆注系統(tǒng)
隨著托輪規(guī)格的增大,其重量隨之增大,所需鋼液量也大幅增加,而托輪均采用單包澆注,因此澆注時(shí)的直澆口數(shù)量不變,仍為2個(gè),在澆注速度不變的情況下,澆注時(shí)間則大幅增加,由此導(dǎo)致橫澆口和內(nèi)澆口的過鋼量也顯著增加。如φ2 200 mm的托輪鋼液總重達(dá)到35 t左右,約為φ1 800 mm托輪的1.8倍。由于澆注時(shí)過熱鋼液長(zhǎng)時(shí)間流經(jīng)底面的橫澆口和內(nèi)澆口,急劇加大了該處的過熱量,形成負(fù)溫度梯度,從而加大了底部對(duì)應(yīng)內(nèi)澆口部位出現(xiàn)縮松的風(fēng)險(xiǎn)。上述縮松嚴(yán)重時(shí),在粗加工后無損檢測(cè)即可發(fā)現(xiàn),當(dāng)相對(duì)較輕微時(shí),則在后續(xù)調(diào)質(zhì)過程的高應(yīng)力狀態(tài)下擴(kuò)展成為裂紋。
根據(jù)上述分析,應(yīng)盡量減少底面澆注系統(tǒng)對(duì)托輪本體的熱影響。一方面橫澆口擺放時(shí)按矩形設(shè)置,避免沿托輪周向擺放,減少橫澆口和托輪本體的重合度。另一方面加長(zhǎng)內(nèi)澆口的長(zhǎng)度,可多增加一段磚管,拉大橫澆口與托輪本體的距離。
托輪開裂的裂紋形態(tài)細(xì)直,毛坯狀態(tài)下裂紋在冒口面沿徑向方向橫向貫穿,加工后則在軸孔內(nèi)沿軸向暴露,為典型的應(yīng)力導(dǎo)致貫穿開裂。且從毛坯狀態(tài)下發(fā)現(xiàn)的裂紋來看,裂紋走向正對(duì)切割冒口時(shí)的割口位置,因此可判定冒口切割應(yīng)力是裂紋產(chǎn)生根源。一方面,隨著托輪規(guī)格的增大,冒口尺寸也隨之增大,普遍超過1 000 mm,因此切割冒口的時(shí)間顯著加長(zhǎng),切割過程應(yīng)力累積過大。另一方面,工業(yè)生產(chǎn)中為了保證經(jīng)濟(jì)性,往往一爐裝多件托輪,導(dǎo)致先切割冒口的托輪需要等后續(xù)的托輪冒口切割完畢后才能一起裝爐回火,其在切割完畢后至裝爐回火時(shí)間間隔過長(zhǎng),應(yīng)力無法得到及時(shí)緩解。再次,由于托輪的結(jié)構(gòu)形狀,本體無合適吊耳,在水平切割完冒口后,還需翻轉(zhuǎn)放倒,使用鋼絲繩從減重孔內(nèi)穿過進(jìn)行起吊,極大地拖延了裝爐回火的時(shí)間。
根據(jù)上述分析,為避免托輪開裂,應(yīng)盡量降低切割冒口時(shí)的應(yīng)力,同時(shí)應(yīng)采取有效的消應(yīng)力措施。大型托輪在冒口切割時(shí),不得沿一個(gè)割口割完,應(yīng)采用摳、磨、對(duì)火等方案多次變換割口位置,避免應(yīng)力在同一方向集中。必須保證切割起始及終了溫度,同時(shí)一次性割完,中間不得停頓。切割完的托輪,冒口不要急于吊走,可利用切割余熱緩冷2 h,實(shí)現(xiàn)自回火。托輪在切割冒口時(shí),先置于料盤上,后續(xù)裝爐時(shí)移除冒口后可直接起吊料盤裝爐,縮短裝爐時(shí)間。
按照以上優(yōu)化措施,后續(xù)所生產(chǎn)的上百件大型托輪質(zhì)量得到顯著改善,避免了重大缺陷,極大地降低了返修成本并縮短了返修周期,取得了顯著的經(jīng)濟(jì)效益,如圖9所示。
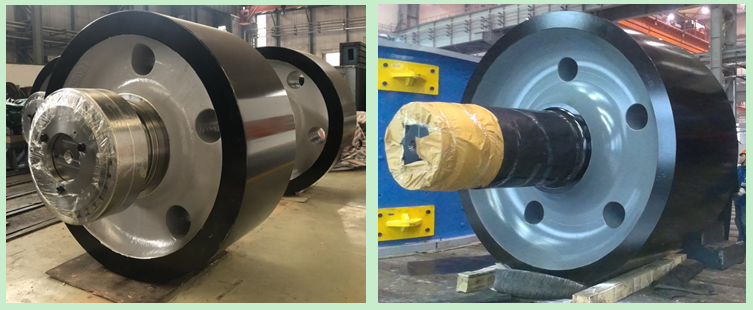
(1)合理的澆注速度控制和出氣措施可避免出現(xiàn)憋氣、夾砂等缺陷。(2)大型托輪在結(jié)構(gòu)設(shè)計(jì)時(shí),凹槽深度盡量控制在150 mm以內(nèi),最大不得超過200 mm。若鑄造企業(yè)無法變更原始設(shè)計(jì)尺寸時(shí),可結(jié)合實(shí)際條件適當(dāng)增設(shè)工藝補(bǔ)塊,來滿足補(bǔ)縮通道要求,后續(xù)通過加工去除以滿足圖紙尺寸。(3)隨著托輪規(guī)格的增大,外圓冷鐵的厚度也應(yīng)相應(yīng)增大,以進(jìn)一步提高其激冷效果,強(qiáng)化末端區(qū)的溫度梯度,改善補(bǔ)縮條件。(4)擺放澆注系統(tǒng)時(shí),適當(dāng)延長(zhǎng)內(nèi)澆口的長(zhǎng)度,拉大橫澆口和托輪本體的距離,減少澆注過程中由于橫澆口內(nèi)鋼液長(zhǎng)期流動(dòng)的過熱對(duì)托輪本體的影響。(5)大冒口切割時(shí),應(yīng)多次變換割口位置,避免應(yīng)力在同一方向集中,同時(shí)要一次性切割完畢,切割后應(yīng)及時(shí)入爐回火去除應(yīng)力。